What’s a Full Service? Part 4: Casing & Quality Control
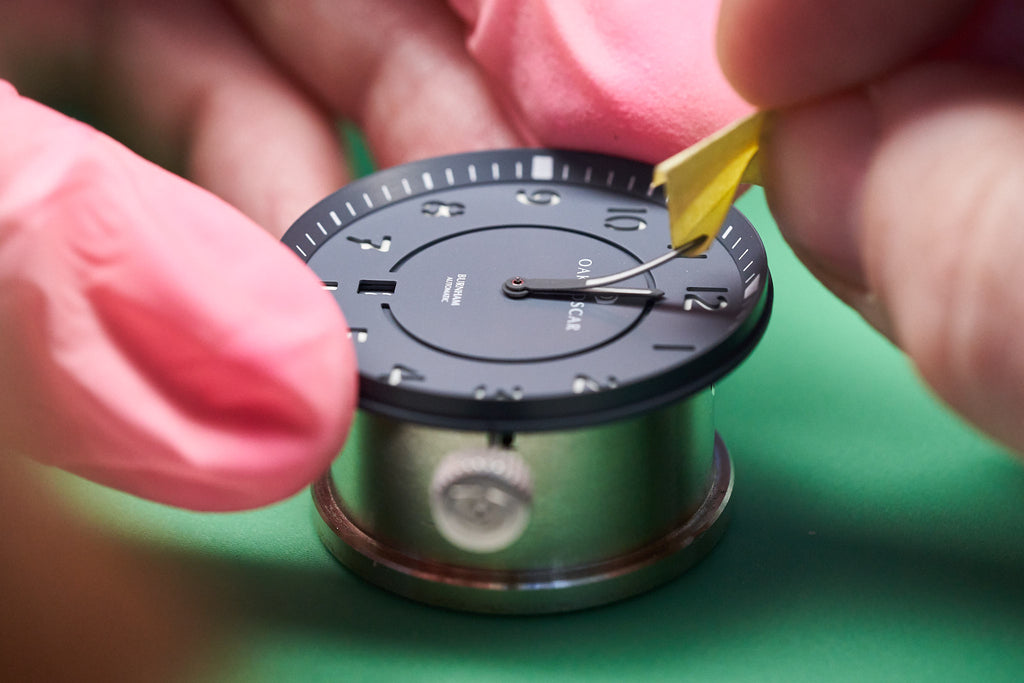
A perfectly-serviced movement is a thing of beauty, but it’s no good to you unless it’s re-cased on on your wrist. That’s the last part of the full-service process.
Once the movement is fully assembled, complications and all, the dial and hands can be installed. Dials are held to the movement by their “feet,” which extend into the mainplate and are secured by screws or clamps.
Hands are simply pressed into place with a hand-setting tool. There’s nothing to hold hands in place besides friction on their wheel, post, or pivot, so it takes a firm press to fully seat them. To avoid any distortion to the movement or its components, a dedicated casing movement holder with adjustable posts is used to support the movement from below. Without the support posts, you could press a jewel completely out of the movement!
Watches with date functions are carefully set so that the date “jumps” as close to midnight as possible. Hand alignment can’t be adjusted after the fact, so it’s important to make sure that everything is lined up before moving on.
Once everything is together, it’s time to make sure that the dial, hands, and crystal are spotlessly clean. Dust on the dial won’t stop the watch like it will in the movement, but no one wants to look at it on their wrist! Small debris can be blown away with air, bigger debris can be picked up with dedicated sticky tools.
Gaskets are renewed or replaced, the watch is sealed up, and it’s pressure tested. Once the watch is through all of these steps, it’s finally time for quality control (QC).
We put service watches through a rigorous, multi-day testing program to make sure that they’ll keep time as well on your wrist as they do in the shop. That means testing the watch in a variety of positions, both static and dynamic, to make sure that the timing is consistent with the way it will be worn on the wrist.
Automatic watches are also tested for winding efficiency, and all watches complete a power reserve run-down test. A failure at any point in the multi-day QC program means that the watch goes back to the bench for re-evaluation.
It takes nearly a whole week to do these tests! We really want to be sure that your watch is working well before sending it home.
After all of this, once the watch officially passes all the tests, it’s time to ship it home. We guarantee our services, so if there are any issues—hey, nobody’s perfect!—we’ll make it right.
This is the final entry into a full service treatment at Oak & Oscar. Read the first three parts at the links below, or contact us with any questions.
- Part 1: Disassembly
- Part 2: Epilame and Pre-Assembly
- Part 3: Asembly and Lubrication